- Home
- CDMO Services
- Particle Engineering
CDMO Services
Particle Engineering
Particle engineering is increasingly utilised in the pharmaceutical industry for several reasons. A key one is the increasing number of drug substances that exhibit low solubility and hence poor bioavailability.
EUROAPI has the capabilities and expertise to apply particle engineering to active pharmaceutical ingredients and excipients.
EUROAPI can cover your particle engineering needs, mastering two complementary technologies:
- Micronization from development to commercial-scale operations, inhalables and nanoparticles
- Spray drying from development to large commercial-scale output – EUROAPI has the largest pharma spray dryer in the world
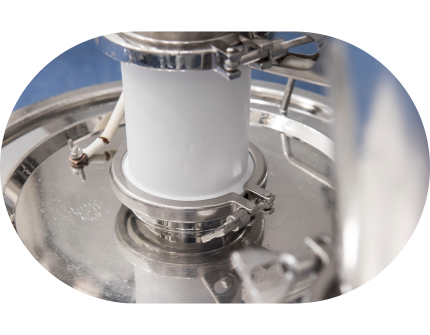
For more information about our Particle Engineering services
EUROAPI particle engineering applications span oral, parenteral and inhaled drug delivery routes to provide the following benefits:
- Improved flow properties
- Encapsulation
- Enhanced dissolution rate and solubility of drug compounds (bioavailability)
- Generate particles with the right ‘aerodynamic diameter’ for effective nasal and lung delivery
Particle engineering technologies are well established and are highly flexible:
- Ideal for ‘difficult to dry’ products – simplify the process if drying from solution
- More energy efficient than other drying technologies
- Good for substances with poor thermal stability
- Precise control of particle size
- Ease of industrial scale-up
- Cost-effective and well-known manufacturing processes
- EUROAPI has capabilities ranging from a few grams to multi-hundred metric tonne scale
We can provide standard and bespoke particle engineering services as part of our drug substance and drug product intermediate development and manufacturing services.
Phase-appropriate particle size reduction processing, spray dryers are in place to advance your compound from concept to clinical and commercialization.
Micronization capability
Particle size reduction to precise particle size distribution is in place for API milling via jet mill and nano-mill processing at our Vertolaye (FR) site.
The EUROAPI Vertolaye site has a known expertise in micronization of API's using the jet milling technology for more than 40 years, and currently micronizes in routine production more than 30 different API's.
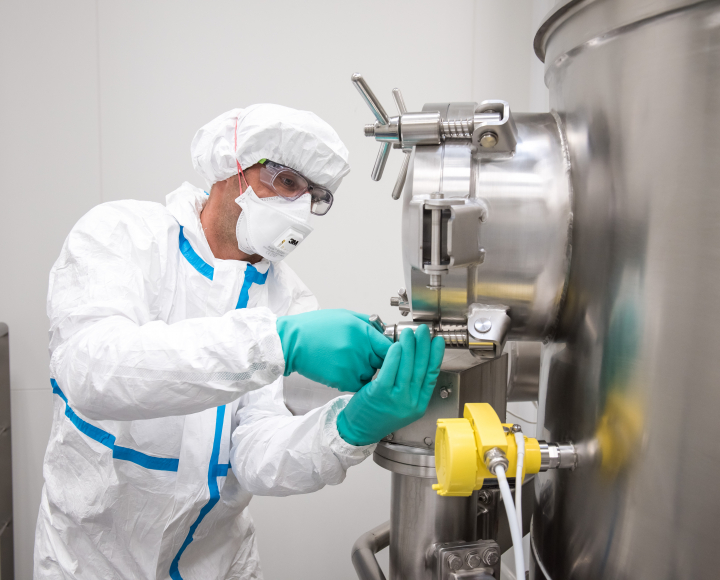
Spray drying capability
Particle engineering services using spray drying, are provided at our Haverhill (UK) site.
EUROAPI has the widest range of pharma spray drying scales available on the market.
The EUROAPI Haverhill site in the U.K. is our Center of Excellence for spray drying with over 20 years of experience in development and commercial activities.
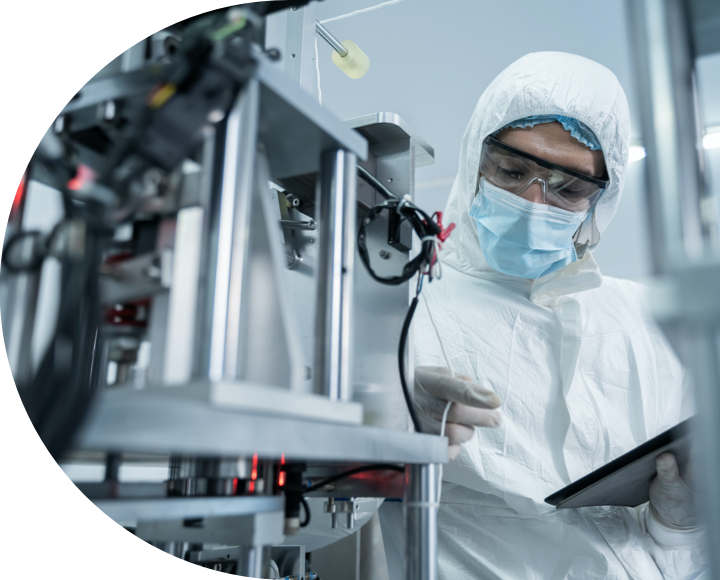